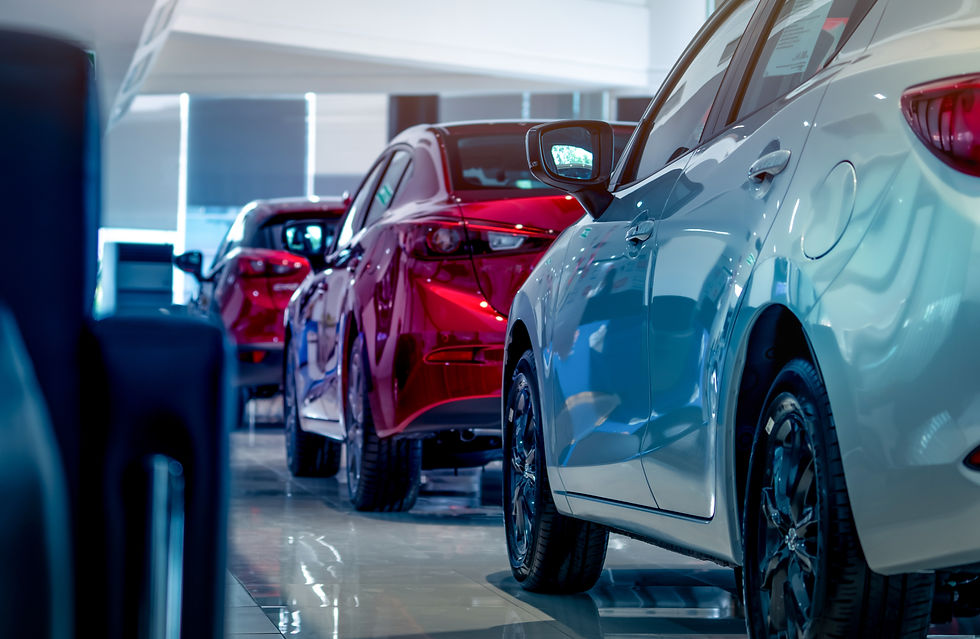
Hand Safety in Automotive Component Manufacturing

Introduction
The automotive component manufacturing industry presents significant risks to hand and wrist safety. According to the U.S. Bureau of Labor Statistics (2020), about 25% of all injuries and illnesses in this sector are related to the hands and wrists. Furthermore, a research article published in ISHN highlighted that 70% of hand injuries were due to not wearing gloves, while the remaining 30% were caused by improper glove usage. Despite these alarming statistics, OSHA's general requirement for hand protection does not provide specific guidelines tailored to the automotive industry.
Unseen Hazards and Long-Term Effects
The risks associated with automotive component manufacturing extend beyond the immediate physical dangers. Workers are exposed to various unseen hazards that can have long-term health implications:
Chronic Skin Irritation - Prolonged exposure to compounds such as hexamethylene diisocyanate (HDI), plastic resins, and aromatic hydrocarbons present in primers and adhesives can lead to contact dermatitis.
Carcinogenic Risks - Some chemicals used in the automotive industry, such as styrene block-copolymers found in adhesives, are potent carcinogens that are readily absorbed through the skin, posing a significant cancer risk to workers.
Defatting and Cracking - Volatile organic compounds (VOCs) such as heptane, xylene, and acetone, commonly used in reducers, degreasers, and paint systems, can dissolve the skin's protective lipid barrier, leading to defatting. Alkaline and acidic solutions used in degreasing and phosphating of body panels can cause severe skin corrosion.
Musculoskeletal Disorders (MSD) - Prolonged use of vibrational tools, grips, pliers, and the manual handling of heavy-duty lifts or hoists can result in persistent muscle-related issues in the wrists, fingers, and palms. Long-term exposure to these conditions can lead to white finger syndrome, carpal tunnel syndrome, and paresthesia.
Array of Risks
The manufacturing of automotive components exposes workers to various mechanical, thermal, and chemical risks.
Mechanical Risks
Cuts, Punctures, Lacerations, and Snags - These injuries occur when handling sharp tools, raw materials, and components such as metal sheets, glass panels, and sharp protrusions of components. Metal debris from lathe machines also poses a significant risk.
Abrasions - These are common during the inspection of components and surfaces by touch, or when sanding by blocks for sharpening.
Crush Injuries - These occur when handling and lifting heavy components and tools like hammers and chisels.
Impacts and Knocking - These risks are prevalent when working in confined areas, such as during component assembly in tight spaces.
Thermal Risks
Handling high-temperature materials and tools, such as those used in welding or heat generated in casting foundries, can result in thermal injuries.
Chemical Risks
Chemical exposure in automotive component manufacturing can occur through immersion, intermittent contact, or splashes. The complexity of chemical products, which are often mixtures of various ingredients, can lead to unpredictable behaviors compared to their parent substances. Additionally, chemical permeation charts and ratings, while useful, may not always reflect the actual exposure risks in the manufacturing environment.
Conclusion
The automotive component manufacturing industry presents a complex array of risks to hand safety, ranging from mechanical and thermal hazards to chemical exposure and long-term musculoskeletal disorders. Understanding and mitigating these risks is essential for ensuring worker safety and productivity. By implementing proper hand protection strategies and staying informed about the specific dangers present in the industry, safety managers can better protect their workforce from both immediate and long-term injuries.